Jorge Robles Verdecia
Mª Nieves Medina Martín
Centro Español de Metrología
El par de torsión está presente en nuestro día a día. Básicamente, en todo proceso donde intervenga un motor o un generador, donde se genere una fuerza mecánica, esta magnitud está presente y su medición adquiere una relevancia fundamental. Ello incluye ámbitos muy dispares relacionados mayormente con la industria, la salud o los transportes. Sólo por citar algunos ejemplos concretos, se incluyen los siguientes:
- Bancos de prueba de la industria, por ejemplo para motores (combustión, eléctricos, hidráulicos,…)
- Componentes de automóviles como limpia parabrisas, ventanillas eléctricas, embragues, dispositivos de arranque, apriete de ruedas etc. (Véase la figura 1)
- Implantología bucal. (Véase la figura 1)
- Control y monitorización de procesos, por ejemplo, para el control de viscosidad en agitadores de mezclas o el control de velocidades de corte en máquinas herramientas.
- Sistemas de generación y transmisión de potencia, donde es fundamental conocer con precisión los valores de par de torsión y de velocidad de rotación para optimizar estos sistemas, por ejemplo, en los aerogeneradores
- Montajes mecánicos de piezas.
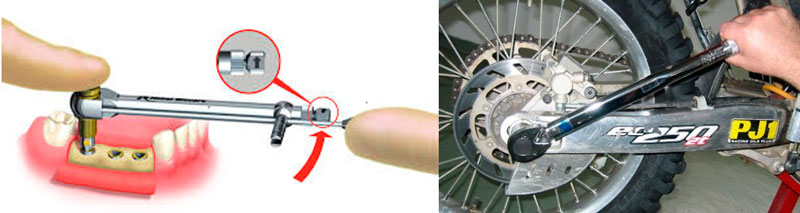
Para muchas personas la denominación “par de torsión” no es muy conocida; quizás si se habla de “torque”, mucha más gente esté familiarizada con dicho término que, en realidad, se trata de un anglicismo.
El par de torsión es una magnitud derivada y se define como el producto de una fuerza tangencial por la distancia entre su punto de aplicación y un centro de rotación. Su unidad en el Sistema Internacional de unidades (SI) es el N·m. Esquemáticamente quedaría representado de acuerdo a la siguiente figura (véase la figura 2):
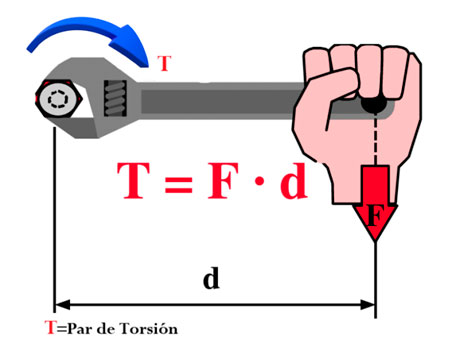
El par que debemos aplicar para cada tornillo o tuerca viene determinado por los fabricantes de los mismos y dependerá fundamentalmente de su métrica y la calidad con que esté fabricado. El objetivo final es conseguir una correcta sujeción de las piezas que une el tornillo, sin someter el material a una tensión extra. Un par de apriete insuficiente implica un riesgo de desapriete, y un par excesivo puede llegar a deformar las piezas ensambladas o incluso acabar en rotura. (Véase la tabla 1).
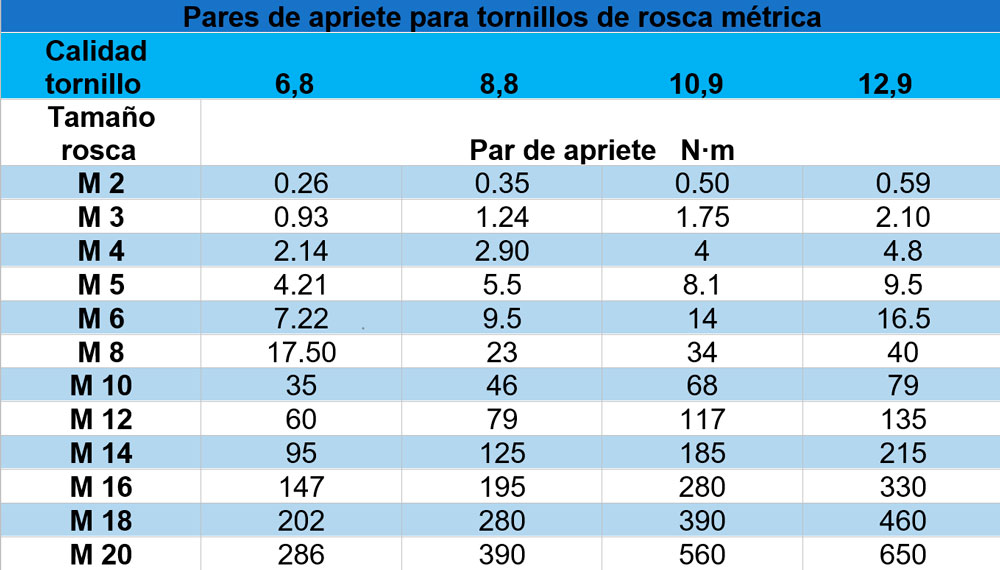
Aunque el método tradicional de apriete “al tacto” es ampliamente usado, es aconsejable respetar los valores recomendados por el fabricante, para obtener el mejor resultado y esto solo se consigue usando una herramienta o llave de par.
Los criterios que han de cumplir estos instrumentos se encuentran recogidos en la norma UNE EN-ISO 6789: 2019: “Herramientas de maniobra para tornillos y tuercas. Herramientas dinamométricas manuales”. De acuerdo a esta norma pueden ser clasificadas en tipo I (indicación a través de una escala mecánica, un dial o visor digital) y tipo II (herramienta que se pre-ajusta a un cierto valor de par, de forma que, cuando se alcanza el valor de par prescrito, se escucha una señal de una forma audible, perceptible o visible). (Véase la figura 3).
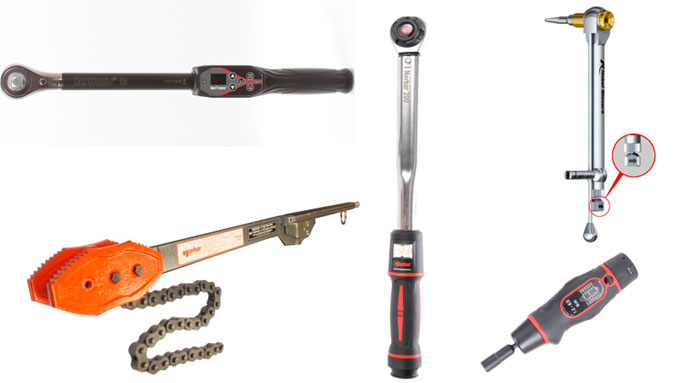
Para realizar un par de apriete adecuado, se deben cumplir rigurosamente estos dos pasos:
1. Aproximación: Siempre se realizará en estrella, esto es, apretando primero una tuerca y luego la de enfrente, en lugar de la contigua. Se puede usar una herramienta que tenga un par fijo en el ajuste más bajo (el par de apriete de la herramienta no debe exceder el par requerido) o llaves con una función de limitación de par, que garantizarán que no se sobrepasa el par requerido.
2. Apriete. Siempre en estrella también. Apretar las tuercas hasta su valor requerido, utilizando la herramienta o llave para garantizar el par de apriete correcto de cada tuerca.
Cumpliendo estos dos sencillos pasos, se asegura un buen contacto entre los elementos que queremos unir.
La calibración de las herramientas y llaves de par es esencial para mantener la fiabilidad de las medidas y garantizar su precisión y repetibilidad en el tiempo. Ello es vital para lograr que estos instrumentos proporcionen las lecturas correctas y aseguren la generación de los pares de torsión adecuados. La norma UNE EN-ISO 6789:2019 establece cómo se deben realizar dichas calibraciones (véase la figura 4).

La frecuencia con la que se debe llevar a cabo la calibración dependerá fundamentalmente de factores de utilización como la precisión requerida, el tipo de uso, la frecuencia de utilización, el medio donde se desarrolle, etc. Estos requerimientos deben quedar por escrito en procedimientos de control y pueden variarse dependiendo de la evaluación de los resultados de calibraciones sucesivas. Si no se aplican procedimientos de control, la norma UNE EN-ISO 6789:2019 recomienda un valor por defecto para el intervalo de recalibración de un periodo de utilización de 12 meses o 5.000 ciclos aproximadamente, lo que ocurra primero.
Comentarios